Dallas / ft. worth chapter mtfca established 1974
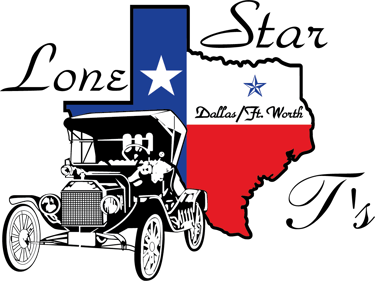
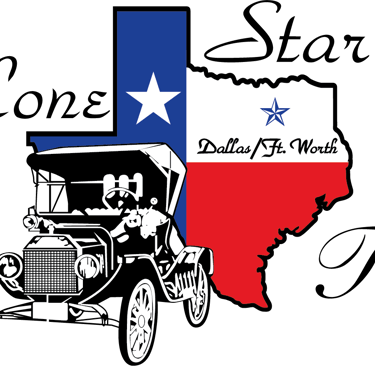
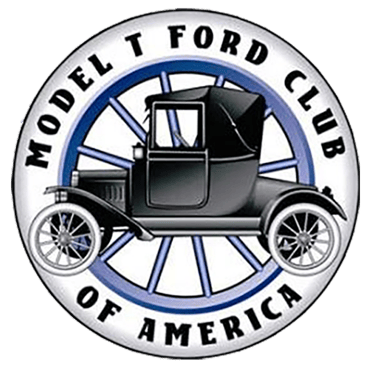
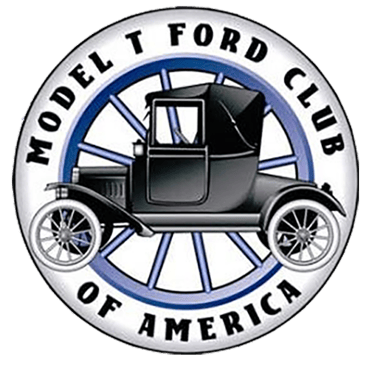
Wheels and Tires
Adjusting Front Wheels
Take off hub cap, remove cotter pin nut and spindle washer. Adjust bearing so that the wheel seems to bind; give the wheel a few turns to be sure that all the working parts are in perfect contact; then back off the bearing ¼ to ½ turn, which will allow the wheel to revolve freely without end play.
To determine if there is end play, grasp the spokes and shake the wheel. Do not mistake loose spindle bushings for loose bearings. Insert a cold chisel between axle and spindle to take up any play while testing the bearings.
Next, put on spindle washer and nut, drawing the nut to a firm bearing. Make sure that the bearing has not been forced out of adjustment. This can be determined by giving the wheel a few turns. Insert the cotter pin which locks the nut on the spindle, fill the hub cap with grease and screw it in place on the hub. (Ford Instruction Book)
Balancing the Front Wheels on a Model T
When Model T's were originally produced, roads were poor at best and highway speeds seldom exceeded 40 mph. With today's roads and the modern technology used in today's restorations it is not uncommon to have a Model T capable of speeding down the highway at speeds in excess of 50 mph.
Once past the speed of 35 mph, the front wheels can begin to bounce and wander, which can be a direct result of being out of balance. This condition will wear out a set of tires extremely fast and will make the car very uncomfortable and unsafe to drive. The solution to the problems is very simple. Go to your local tire shop and purchase a flat weight used in balancing "mag" or aluminum wheels. This type of weight has an adhesive tape on one side so no holes need to be drilled. Jack up the front end and loosen the front wheel bearings so the wheel turns VERY easily. Now, spin the wheel/tire and note where the wheel/tire stops. Usually, the valve stem will rotate to the bottom, closest to the ground, every time. This is especially true if you have metal valve stems and caps. Spin the wheel/tire again. If the wheel stops in the same place as in the first spin, you have a heavy spot and an out of balance wheel. You will need to place weight on the opposite side, or 180 degrees away from the heavy spot on the wheel. Spin the wheel again and note where the wheel stops. If the wheel stops in various locations after it has been spun, you have just "balanced" your wheel. If it stops in the same location as before, add more weight until there is no pattern when the wheel stops.
This sounds like a "backyard" fix, yet I did this to my '13 touring and found it to work extremely well. From the day I finished the restoration on the car, the front wheels "wobbled". I wore out tires and didn't feel comfortable driving down the road. Now the annoying wobble and shimmy are GONE, the car drives smoother than it ever has. (Russ Furstenow T-Time in Canyon Country reprinted in LST News 2000)
Easily Install New Clincher Rim Tires ... Clinching is a Cinch
Don't pinch that tube! Mounting clincher tires doesn't have to be the misery some people make it. Follow a few simple rules and mounting a clincher is a cinch!
First get a bucket of soapy, sudsy, water. Do your mounting on grass or an old piece of carpet to reduce damage to the paint. Always mount the tire from the back or inside of wheel or rim. That way any paint to be touched won't be so apparent. Using a small sponge (or cloth), soap the clincher portion of the tire on the side to be mounted first. Using a tire iron, pry it over the rim being as careful as possible with the paint. It should be noted here that although it's more work, tires can be mounted by pounding them on with a hammer. Either way work your way around the rim until one side is on.
Next insert the tube; pulling the stem through the hole to full length. Then pump in just enough air to make the tube nice and round. This is the KEY to preventing pinched tubes (the rounded tube surface is difficult to pinch).
Next, sponge some suds on the other side of the tire and pry (or hammer) into place. At this point the rubber clinchers may not be fully seated into the rim. Seat them by striking into the tread of the tire with a large hammer.
Next, start airing up the tire, again striking the tread at any point around the rim where the clincher isn't seating well. Finish the job by touching up any chips or scratches to the paint and be sure and put in at least 40 to 50 pounds of air before driving (otherwise the rear tires may slip on the rim when you apply the brakes). (Fred H. (From the T-Bone Times, March 1980)
SIMPLE METHOD OF STRETCHING NEW CLINCHER RIM TIRES
A rather simple method of stretching new clincher rim tires came to mind while reading the Model T Times. Since the biggest problem is that new tires seem to be manufactured "too small" for the rim, the solution would be to stretch the tire. Here is how to do the stretching without damaging the tire. Take the spare out of your car. If the inflated diameter is around 24", you're all set. Let the air out of the spare tire and put the new clincher tire round the outside tread of the deflated tire. Put air back into the spare tire and watch the clincher tire bead stretch. Finally put the tire(s) in the sun for a day. After sitting in the sun, the clincher tire will "fall" onto the clincher wheel and the new tire will not be damaged in the process of stretching. (Russ Furstenow, From T-Time in Canyon Country)
INSTALLING A CLINCHER 30 X 3 1/2 TIRE WITHOUT TIRE IRONS
As we toured on the national tour this summer, it became apparent that the number one nemesis of the Model T's on the tour was flat tires. From what I could tell, pinched tubes were the cause of many tube failures. In 1966, I was taught how to install a tire properly by using only a rubber mallet. The mallet is designed for tire use and has some weight in the head of the hammer and has a long handle.
Start with a clean rim and a good tube and tire. Inflate the tube until it just takes the shape of the tire (not too much air). Place the tube into the tire and then place the valve stem of the tube into the hole in the rim. Place the rim and tire onto the ground and push both inner and outer beads of the clincher tire onto the rim. Be careful so as not to have the valve stem become crooked in the hole by alternating where you hit the tire in relation to the valve stem (hit the tire on one side of the valve stem and then hit the other side). Once you have the tire mounted, inflate the tire to 2 pounds and let the air out of the tire. This is to "seat" the tube. Do this a couple of times. Finally, install the valve core and inflate to 55-60 pounds.
By using this method, you never have the possibility of pinching the tube with a tire iron, and a future flat. I have some tires that have the "original" 1966 air in them as proof. (Russ Furstenow , From T-Time in Canyon Country)
Felt Seal for Front Wheels
Number 2809 felt seal is used in the front wheel inner grease retainer. Did you know this felt is also used as a rear wheel seal? It fits in a groove in the rear wheel hub and helps seal the outer wheel bearing. Also helps keep the steel cup from coming off the housing. Put a few drops of oil on it to keep it from scorching. (Contributor Unknown)
Preventing Grease From Working Into the Brake Drums of the Ford Rear Axle
A good many Ford owners are having difficulty in keeping the grease in the differential housing of the Ford rear axle from working out into the brake drums and impairing the efficiency of the brakes. This difficulty can be eliminated by boring a 3/16 -inch hole half way between the differential housing and the brake, found at the loose part of the axle. When the grease reaches the holes, it will run out here rather than continue on through the axle housing and the brake drums. ("Stewart Lever", October 1916 - From T-Time in Canyon Country)
Removing the Rear Wheels
A properly tightened rear wheel hub is difficult to remove from the axle. The so-called knock off wheel puller, now sold in parts stores is practically useless. It may even cause serious damage. The Model T wheel puller, furnished by Ford in the tool kit with all new cars, is one of the best tools for the job. If you do not have one, try to buy one at a swap meet, if at all possible. The type used for the wood spoke wheel models is screwed onto the hub in place of the hub cap, then clamped tight on the threads. The wire wheel type engages a groove in the hub. Either type has a screw which is tightened against the end of the axle. Usually, several sharp blows from a heavy hammer on the end of the screw will loosen the most stubborn case. It is helpful to jack up the wheel opposite the one being removed. To prevent damaging the axle end and threads, the axle nut should be flush with the end of the axle. If the correct puller is not available, a gear puller which can be bolted to the hub with the lug nuts will work on the wire wheel models. For wood wheel models, try loosening the axle nut about 1/2 turn, and drive around the block. (Hugo Richter)
Tubes, Rim, Flaps, and Wheels
After all the flat tires I had on the tour, I decided to replace the existing tubes with new tubes. The dilemma I had was how to take off and replace the tires without badly scratching and nicking the newly painted rims. The solution was simple.
I put black friction tape over the tire iron where the iron would/could come in contact with the rim and also put friction tape around the rim itself. The result was no nicking or chipping of any paint!
Another problem I noted was the tire flaps placed in the tire to protect the tubes had folded in some places, making heavy spots and creating possible pinches in the tube. Flaps are not cheap (around $10); they are a bear to install and I wasn’t satisfied with the folding I noticed. What to do? A cheap and easy solution was to make "new" rim liners by taking an old 15" tube and cutting the tube into strips. Here is what to do:
Cut a hole in the tube about 1" away from the valve stem. Now take a pair of scissors and make a cut the entire circumference around the tube. Now cut another hole 1" away from the valve stem on the other side of the valve stem. This allows the rim liner to be about 2" wide. Now make a cut around the circumference, which parallels the first cut. Cut the valve stem out of the tire, make a round hole where the valve stem was, and stretch the "flap" over the rim placing the hole where the stem was on the rim where the tube valve stem will go.
The rim liner has virtually no weight and the tube will never come in contact with the steel rim. This is far superior to using duct tape on a rim, which I have seen done on many occasions. Using one old tube, you can usually get at least 5 to 6 rim liners. (Canyon Country Model T Club's Newsletter)