Dallas / ft. worth chapter mtfca established 1974
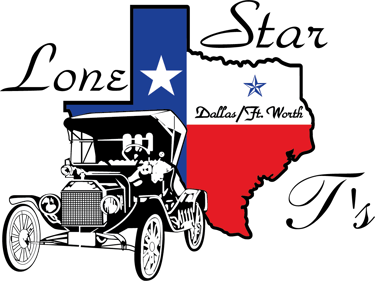
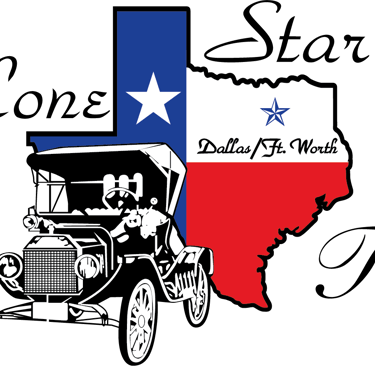
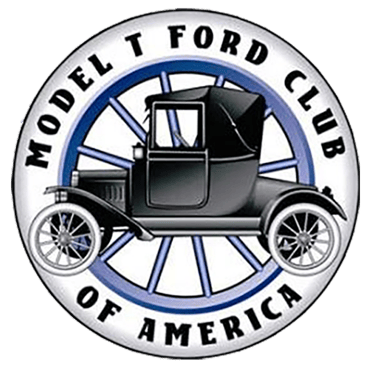
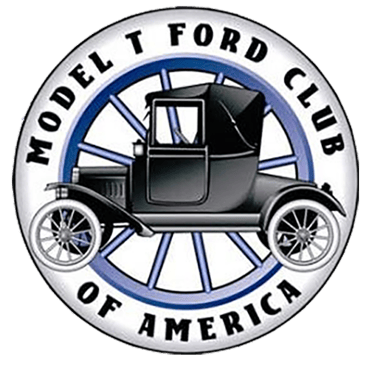
Engine & Transmission - Part 1
Air Cleaner Assembly & Engine Sealing
Henry Ford's marvelous car was designed in a era where trips were short, the speed low, and the driver was expected to pay close attention to the maintenance of his mechanical steed. Today we drive our T's long distance, at high speeds, and we are used to the relatively maintenance free modern car.
One of the best ways to improve the longevity of any car engine, particularly one that is being worked hard (Model T going 45 mph), is keep the guts of the engine CLEAN. This means an air cleaner, and sealing up the other holes that allow dirt to enter the engine interior.
The later model T's have more room under the hood than the early cars. I don't think this installation will work on the brass era cars. I installed a Briggs & Stratton washable foam air cleaner which was used on a 8 hp industrial engine. The base of the air cleaner was a slip fit on a short length of exhaust pipe tubing. The tubing was welded to the top of a cut down Model T hot air tube. The completed assembly mounts to the hood clash strip using a existing hole, so no permanent modification was necessary.
For those who aren't inclined to build their own, there is a line of very popular washable screen air cleaners made by the K&N Company which are use in motocross motorcycles. Several of these look as though they would fit in the confined space of a Model T engine room. These filters have a rubber tube molded into the base which slips over the carburetor inlet. No modification to the T carburetor should be necessary. See your favorite motorcycle dealer.
When the pistons are going up and down inside the engine, they cause air and dirt to cycle in and out of the crankcase. This air is pumped through any of the available openings, which in the case of the T are the oil filler cap and the two holes which allow the throttle rod to pass through the block. I filled the cavity inside the top of the oil filler cap with a chunk of open cell foam. The valve cover has a thin piece of the same foam sandwiched between the cover and the gasket. This has a slit in it to allow the throttle rod to pass through.
The last hole to plug was in between the number 2 and 3 cylinders. This was done by using a third piece of open cell foam which was glued to the cylinder block on the inside of the engine. This piece also has a slit to allow the throttle rod to pass through. The adhesive used was RTV silicone, but any good gasket adhesive which will stand up to the oil will work. (Contributor Unknown)
Adjusting Transmission Bands
To adjust the transmission brake bands quickly, place a tire iron, or a screwdriver, against the transmission band washer, and pry the lugs of the band together. Then the nut on the transmission band screw can be easily tightened or loosened with the fingers. Care should be taken to lock the nut with the washer; having the projection on the washer engage the groove on the nut.(Author Unknown)
Building an Early Type Drive Shaft
I have recently built an early style driveshaft for my 1917 “T”. The trouble all began when I tried to mesh the ring gear with the pinion gear. I couldn’t get the pinion gear to go in far enough. Upon inspection I found I had overlooked the fact that an early style driveshaft bearing housing is longer than the later style. I had to disassemble the driveshaft and face off the housing to the correct length. The reason the early style is longer is because there is a ridge on early rear end housings which fit into the veering housing which is not on later style housings. (Nolan Renfro)
Changing Connecting Rods
Ford connecting rods can be changed, without removing cylinder head! Remove cap from lower end of connecting rod. Pull piston down until bottom ring snaps out of the cylinder. Take cotter out or piston pin clamp screw. Remove piston pin clamp screw with a Tee-Wrench.
Piston pin can usually be pushed out with fingers. But if not take 14 inches of 5/16 inch steel rod and bend it L-shaped, with the 2-inch short end at right angles with the 12-inch long end. I'ut a nut on the short end of this pry bar, and use it to force out the piston pin.
To replace the lower piston ring in the cylinder, compress the ring with a scissors type of ring squeezer, which can be bought or made up in the shop. Removing spark plug makes it easier to push the piston up into cylinder.
Have used this method for over two years, making average tie of 35 minutes per connecting rod. (Ford Dealer and Service Field, June 1926 - From Frank Martin, Conshohocken, PA)
Check That Oil with a Dipstick
It's no secret - especially as we get older (and some of us have already long passed that point) - that checking the oil can be a real pain in the back. Who among us hasn't already rigged up a long rod with some gadget to open the oil cocks. And sure there is the $16 sight gage - but you still must get down and kinda' under. I'll be happy to sell you mine. The dip stick is the answer; Why didn't Henry think of it?
Now you can go buy one for 26 bucks, but the real T imagineers never buy anything that can be rigged from parts around the shop, picked up for next-to-nuthin' at the last swap meet, or found down at the local hardware store. here's what's working well for me - and cost me less than a case of diet coke on sale. And it's an easy Sunday afternoon project.
Get a dipstick from about anything. Mine was a nice new chrome one from a 454 Chevy - $2 at Pate. You're going to cut it pretty short anyway, so the length is not important. Remove the crank case oil cock (T3079N for the purist) and take it and your dip stick to your hardware store. Use the upper oil cock to reduce the oil loss, but eventually you will screw the plumbing into the lower hole. Show the hardware person what you are trying to do, and you will leave the store with three new brass pieces: a tee, a short extension to connect the tee into the hole in the case, and an adaptor that will connect the bottom of the dip stick casing to the tee. The oil cock will fill the third hole in the tee, if you still want it. If not, get an elbow instead of the tee.
You will need to bend carefully the dip stick casing about 70-80 degrees with about a 6-8 inch radius - a loose curve that will allow the dip stick to slide down the tube without binding. Determine where you want the dip stick handle to be (mine is just above the carb) and that will determine how long you want the casing to be. Cut it off before you connect it all together to keep the trash out of the casing and, hence, out of your engine oil. Either bolt or weld a support bracket to attach your casing to one of the engine bolts (not to the body). Stick the dip stick down the casing to see how much you now need to cut off. Taper the end slightly to make it work easier and to reduce wear. I won't insult you by telling you how to calibrate the new dip stick.
That's all there is to it ... except when you have your T out for a tour and all of your friends are standing around, open you hood and pull out your shiny new dipstick. Hold it up as if you are checking your oil. It's a real conversation starter - as if we really needed one? (Glen Campbell. Lone Star T Newsletter November 1996)
I purchased a dip strick that works just great from Lang's Old Car Parts. (Judi Cobb 2025)
Cleaning the Vaporizer Heating Plate
Approximately every five thousand miles it is advisable to remove and clean the vaporizer heating plate. This plate can be easily removed by removing the four exhaust manifold cover screws, loosening the vapor outlet tube nut and moving the cover away from the manifold. Ford Instruction Manual
Crankshaft Counterweights
Ever since my fiber gear shucked its teeth a few months ago I have been living with a metal timing gear. Due to a fitment problem with the camshaft I cannot get the gear to run perfectly quiet. Not the fault of the gear. Yet, the gear noise, which is an intermittent clatter at certain speeds, serves a purpose: It alerts me to the harmonic vibration periods inherent in the T crankshaft. They do exist in every car. But what about my engine?
The repro Dunn-type counterweights are supposed to get rid of vibration. My counterweights were mounted with great care, and then the crank was spin-balanced. I saw with my own eyes the crank spinning several thousand rpm on the Stewart balancing machine. It was perfect dynamic balance. And this is the way I've been running- with some annoying noise as the backlash of the timing gear gets slapped against once or so every other revolution. At around 25 there is a faint clatter. At about 33 mph the noise returns but louder. The clatter passes away upon further acceleration, but at 42 the clatter returns and has become very pronounced. Like a boiler shop. Above 45 the noise disappears again. Interestingly, whenever the clatter is loudest the tension side of the fan belt vibrates visibly, whipping to and fro. The belt whip is yet another manifestation, in my opinion, of the severe harmonic vibration present in the counterweighted crankshaft. The counterweights do not stop harmonic vibration.
So, the question is- do the counterweights worsen the harmonic vibrations?
Only one way to find out: Take off the weights. I did Result: The nasty vibrations are gone. The clatter remains, but MUCH reduced in sharpness. It is present over wider brackets of engine speed, but the noise and belt whip is never so strong as it was with the counterweights.
I have decided of course, that the counterweights are counterproductive. They are permanently retired from service. The weights' large mass caused a tuning effect- where the light harmonic vibrations were damped out, only to be concentrated or amplified strongly at certain critical engine speeds. A mere matter of tuning. What the Model T needs, is a harmonic balancer (damper).
What MY car needs is a better fit of the timing gear. My custom camshaft has small but fatal defect: the shoulder that the gear is supposed to press-fit upon is too skinny by about 10 thou. So the gear cannot be accurately centered- it is a matter of chance and luck when the cam nut is torqued down whether the gear gets moved off center. I need to pull out this $$$ camshaft and have the shoulder built up somehow. Metal spraying? Returning the camshaft is not an option. I like it very much except for this one little defect.
So it goes that one person's mistake (cam shoulder) becomes another person's higher education in the inherent harmonic vibration of the Model T crankshaft! (Reid)
Bear in mind that the T crank is very skinny- which adds to the whipping effect- it's like a spring being alternately coiled and released by the individual explosions. Naturally, the #1 and #1 cylinders can "wind up" the crank more than the other cylinders closer to the flywheel. (Posted by Reid Welch on November 17, 1999 at 22:29:55: Model T Forum Page)
Dead Timer Roller
After all the driving had been done at the last Texas T Party, it was necessary to drive the Model T one more time for this year's picture. The car started with the usual one pull of the crank, ran for a couple of seconds then died as if out of gasoline. Two or three repetitions of this then not a whisper, not a buzz from the coils. The gasoline tank was full just thirty miles earlier. The gasoline had not been shut off. A simple check verified that there was power to the coils from the ignition switch.
The problem was solved by replacing the timer roller and cleaning the timer interior. It seems that the oil had caked around the rivet which forms the axle of the timer roller, effectively insulating the rolling element from the remainder of the roller assembly. No ground, no buzz, no ignition, no start! (Hugo Richter, Lone Star T Newsletter 1988)
Exhaust Pipe Packing Nut
For years, the exhaust pipe packing nut continued to come loose, and the fumes would almost choke me before I could get the engine stopped. Had the nut wired on, and even had holes bored through the angles for wires to be passed through and fastened to screw eye fasteners to side of body to keep nut from turning. Bought a special wrench for screwing up this nut. Had several garage men tighten up the nut, and they always assured me that it would not give further trouble. They put emery, asbestos, fine wire and what-not on the threads –but with no effect.
Had the trouble until a mechanic asked me if I had tried salt. Made a thick paste of fine salt and filled the threads in the nuts and the threads on the end of exhaust manifold and screwed nut up tightly. Has been there a year now and have never budged. (S.R. Howard, Hillsboro, OH)
Fix That Sediment Bulb Fuel Leak
One of the aggravating problems one has with a Model T is a fuel leak. One of the most common fuel leaks can be found where the sediment bulb is screwed into the gas tank. I have found that Teflon tape can be used successfully, but this is not a guaranteed repair. A permanent repair can be accomplished by filling the threads on the sediment bulb with solder. First, remove the sediment bulb and thoroughly clean the threads on the bulb which screws into the tank. Next, once the threads are clean, "tin" the threads with solder. While the sediment bulb is hot, fill the threads with solder and then quench the bulb with warm water. If you have a power wire brush wheel, remove the excess solder so the top of the threads can be seen. Now screw the bulb back into the gas tank and any leaks should be a thing of the past. (Author unknown, From T-Time in Canyon Land ~2000)
Front Crankshaft Seals
Front crankshaft seals can be a bummer on the Model T. If you want to filter those oil drips, just use the felt half-seals that come with the gasket set! However, if you would rather keep the oil on the inside of the engine you need to use the hard white rope seals that are made for the 1938-1948 Ford V-8. These are used with about 100 percent success. Be sure to use a 1 1/4 inch socket to force the seal into position, tapping it quite hard with a hammer. Then use a sharp knife and cut each end off about 1/32 of an inch above the block, also do the same thing to the engine oil pan. You will want to improve the seal by putting a small amount of gasket cement in the groove before putting the seal in the groove. Ask for part number NAPA #5V762. Throw the gasket away and use the two half seals! (Courtesy of Herb Z, Sunflower State Cranker)
Gear Clearance
An easy way to establish gear clearance is to use the four part bill of lading such as used by motor freight companies. Cut the form into strips, and keep the alternating layers of paper and carbon in their original order. Feed the strips between the gear teeth, adding layers until the paper "writes". Measure the clearance, make corrections as needed and repeat the measurement process until the desired clearance is achieved. (Ralph Zajicek)
How I Made a Head Gasket for a Riley Multi-Ford Head
Needing a new head gasket for my Riley multi-Ford head, and discovering that a stock head gasket would not work (the valve portion of the combustion chamber is much larger than a regular Ford head and the valves in this engine are much too large for a stock gasket). I decided I would try my hand at making one. I carried a piece of the old gasket to a local firm that sells and fabricates gaskets and gasket materials. They were able to identify the old gasket as being made of Klingerit 1000. This material is made of two layers of an asbestos like material with a layer of fine mesh wire between them, and is about 1/16 of an inch thick. The first step in making the gasket is to lay the material on the head and with a very small ball peen hammer mark the rear head bolt holes. Punch these out with a gasket punch or very carefully with the head bolts. Then mark and punch out the rest of the heat bolt holes. The next step is to mark the water passage holes and cut them out. The large holes I cut out with a very sharp small wood chisel after making them with the hammer. The small "steam holes" can be drilled with an electric drill or carefully punched out. The next step is the valve and combustion chamber. these can be cut out with the wood chisel. The wood chisel cuts should be made on a piece of smooth hard wood. The last step is to smooth all the cuts up with a small file. The cost of the material was less than $8 and this gasket worked very well with no combustion or water leaks. (Wally Shipley)
Installing a ’26-’27 Brake Drum in an Early Type Engine
It is possible to use the 26-27 type brake drum in an early style engine but there are modifications. The advantage to using the later style drum is because the clutch lugs which wear, and are hard to repair on the early style drums, are replaceable on the later style.
In order to use the later style drum you not only have to have the drum but also the drive plate (or pressure plate) and the six special bolts which attach the pressure plate to the brake drum. The bolt pattern on the later style drum is closer to the center by just a smidgen.
If you want to make use of the wider brake band you have to use the 26-27 type transmission housing. You can install the early style pedals so it won’t be obvious to the casual observer. The early style transmission cover will fit over the wide band but just barely clears. In my own car I turned the drum down to the same width as the early type. (Nolan Renfro)
Installing Hand Crank Bushing (after it is assembled in the engine)
I was asked if it is possible to install the hand crank bushing into the crankcase after it is assembled to the engine. My experience had been with a bushing machined for a light press fit. "No Problem" I said. After hearing a report that this was possible but barely when using a new bushing form one of our suppliers, I recently tried the same thing with a new bushing from a Model T parts supplier.
The first try had to be abandoned because it is impossible to generate sufficient force with simple tools. The bushing as supplied is rolled into a cylinder from thick sheet. The result is a part which is not truly round. It was necessary to machine for a distance of 1-5/16 inches from the end to remove some material from the high spots. Approximately .005 inch was removed. It was possible to install the bushing from the engine end by using a piece of 5/8 inch diameter all thread rod, two nuts to fit the rod, a washer, oil on the threads and two wrenches to fit the nuts. Even so, approximately 100 ft. lb. torque is required to fully seat the bushing. (Hugo Richter)
Irregular Firing (spark plugs)
When one cylinder alone loses power it may often be traced to the spark plugs, especially if they are of different makes and the points are of variable distances apart. The current ay be of sufficient strength to jump across the points which are not over 1-64 inch apart, but those too far apart offer so much resistance that the spark is diminished. It seems reasonable to believe that the use of one make of plugs in all the cylinders of a motor at one time would be most practically in as much as they would be most apt to promote more uniform firing, owing to their similarity of construction. It is possible, however, to adjust almost any combination of different makes of spark plugs so that no difference in the regularity could be detected. (Gas Power Magazine, October 1913)
Main Bearings, Cam Bearings
Main Bearings … Countersink the holes which take oil to the main bearings. This will allow more oil to be available. It will also be a place for lint to build up, so keep your oil changed! (Nolan Renfro)
Cam Bearings … The special bolts which hold the cam bearings in place sometimes will allow the bearings to move causing end play, so you must be careful, and perhaps shim, under the ends or sides to take up "lost" space. Contributor Unknown
Motor & Drive Shaft, U-Joint
When putting the motor and drive shaft back together, pack the grease around the U--joint before assembly. This is much easier than trying to pack it through the grease hole. (Jim Mullen, thru Joe McCreary, from Zack Troxel)
Also, hold the male end of the U-joint with a loop of wire instead of your fingers. If the motor slips, you are not joined to the car by mashed fingers. (John (Three Fingers) Albright)
Mounting Transmission Bands
When mounting new bands, remove the old bands by taking a cold chisel and placing the chisel on top of the old brass rivet, between the steel band and the cloth band. Hit the cold chisel with a hammer and the rivet will "fall out" of the band. When mounting the new band, take a 2"X2" piece of pine and round off one end of the board. Mount one end of the band leaving some overlap of the band material. Place the rivet into the mounting hole and place the band on the end of the piece of pine, allowing the rivet to penetrate the end of the pine board. Then take the band and turn it over and place the head of the rivet on a piece of steel, and with a small ball peen hammer, pound the two ends of the rivet over. Make sure the rivet is "counter sunk" with the ball peen hammer. Do the same thing to the other end of the band and then push the remainder of the band material into the steel band. Do not rivet the and material to the steel band b going around the band in order. (Russ Fustenow, From T-Time in Canyon Country, reproduced in LST Newsletter 2000)
Need New Valves & Don’t Want to Pay a Fortune and Chevy Valves
There is a good supply available and they can be had for little or nothing. Use Model A Ford valves. Check with some of your friends in the Model A Club, they usually have some old valves that are too short or the heads are ground too thin. Model A valves are longer and have slightly larger heads than Model T valves, so if the stems are not worn too much they make good replacement Model T valves. Use the original Ford valves if possible. They were made from austenitic steel (non magnetic). These are extremely hard to drill or cut with a hacksaw. However, once you get a set of these valves installed, your valve problems are over for a long time. (Royce Peterson, Lone Star T Newsletter, 1990)
When installing small block Chevy valves in my T, it was found that the Chevy valve spring retainer had an inner spring seat diameter which perfectly fits the T valve spring. This makes it possible to use the stock Chevy retainer and keepers and avoid drilling a hole in the valve stem. I turned down the outside of the retainers to the OD of the T spring to tighten them up, but this actually isn't necessary. John Wit
Oil Leak – Pedal Shaft
Pedal shaft material: O-ring seal 5/8” O.D., 12/16” I.D., 3/32” wall, Sears 42-22514.
Procedure: Grease pedal shaft with white grease. Slide O-ring on shaft. Insert pedal and pedal shaft into transmission cover. Install pedal support bracket. Simultaneously work pedal as you tighten the bolt and nut. No other modifications required. (Irwin Harris)
Oil Pan Leaks
Don't use lock washers on the bolts which hold the inspection plate on the oil pan. Oil will seep down the threads and leak. I wrapped a little kite string around mine and they don't leak a drop! (Nolan Renfro, From Lone Star Ts News (19??)
Want to keep peace with the wife and get that oily spot off the garage floor in one fell swoop? Well, if your problem is oil leaking past the bolts on the lower pan, this little trick should help.
First, get some ordinary cotton string. Several feet will be needed. Next, squeeze a dab of silicon sealant into your hand, then pull the string through the silicon several times, completely saturating the string in the process. Then, hang the string up to dry. After letting the string dry completely, take your "rubberized" string and crawl under Liz. Ponder for a moment all the drops oil hanging from each pan bolt head and how nice it will be to be rid of them! One at a time, back each bolt out about an eighth of an inch. Wrap several turns of your rubber string under each bolt head, then retighten the bolt. Trim the exposed string ends and proceed to the next bolt, repeating the process until the job is finished. (Fred Houston, From the Tulsa T-Bone Times)
One Method of Preventing a Noisy Differential
The small grease cup, indicated by the arrow, is located slightly to the rear of the universal joint at the upper end of the drive shaft housing, as shown by the arrow in the sketch.
There is a babbit thrust bearing located in this area that controls the longitudinal movement of the drive shaft (end play).
Very few Model T owners realize that this bearing is involved in maintaining the correct mesh of the drive shaft and the differential ring gear. Any slight amount of wear on the collar of this babbit bearing will cause the gears in the differential to become noisy.
It is somewhat a mystery as to why Henry Ford equipped his T’s with this small size grease cup at this very important area where lubrications is most essential. Use a good grade of soft grease and insert a grease cup full to the bearing at least every 200 miles. (Contributor Unknown)
Poor Idle and Low Speed Operation
PROBLEM: Poor Idle and Low Speed Operation
CAUSE: Worn throttle shaft and carburetor body allowing an intake air lead
CURE: Eliminate throttle shaft slop by re-bushing worn shaft and boring car body
The procedure outlined below describes repairs on my Holley NH, but would work on any carburetor.
1) Disassemble your carburetor and determine the correct throttle shaft diameter at an unworn portion. The subject "NH" has a 1/4 inch diameter shaft.
2) Hobby supply stores, like Michael's, stock a precision thin-wall brass tubing in various diameters. The "NH" will need 1/4 inch I.D. tube.
3) Cut with a tube cutter to exactly match the wear on each end of the throttle shaft without interfering with the fit of the throttle plate. Dry fit the bushings and plate now to make sure. Slide the shank of a 1/4 inch drill into the tubing before cutting to provide a backup for the tube cutter. This will prevent crushing the thin walls.
4) Fix the new bushings in place with a two-part mix epoxy. This will be heat and gasoline resistant.
5) Now prepare the carburetor body. Align the body in a drill press vise with a 1/4 inch drill passing through the stock throttle shaft bore with the drill motor OFF. Set the depth stop so you don't drill through. The bottom of the carb casting. Retract the drill, chuck a 9/32 inch bit and drill the bore. If available, a reamer would be a better choice here.
6) Blow out the metal chips, reassemble the carburetor and listen to that "T" idle!
P.S. Replacement oversize throttle shafts are available. The repair described above will also preserve the original appearance of the carburetor. (Hugo Richter)
Premature Retirement
My first Model T retired prematurely because a gasketed joint had not been properly tightened. Can this happen again to me, or anyone? It will happen unless we check and tighten all the gasketed joints before it does. In terms of oil lost, the transmission cover joints top the list. To make things worse, it is easy to overlook the starter mount, the bendix cover bolts and the magneto post. These dispose of oil real fast.
Bolted gasketed joints loosen because the gaskets seem to lose some of their resilience and take a new set. If the bolting is left loose too long, some of the gasket material may be worn away from vibration. If tightening does not work, the only solution is the installation of a new gasket.
When all the rest is done, check the joint at the rear of the block where the transmission cover and pan all meet. A leak here may be cured by packing with cotton string or cord.
Prevention of oil leaks may avoid a trip on the vulture wagon sometime. (Hugo Richter)