Dallas / ft. worth chapter mtfca established 1974
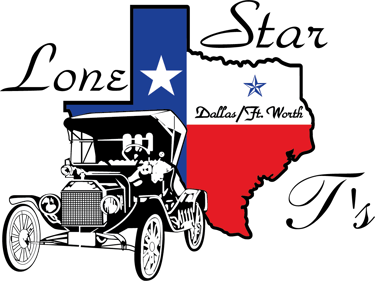
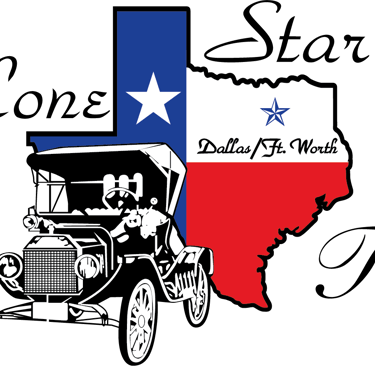
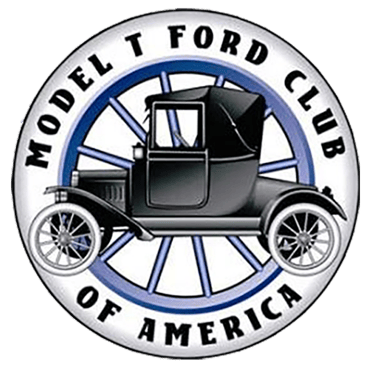
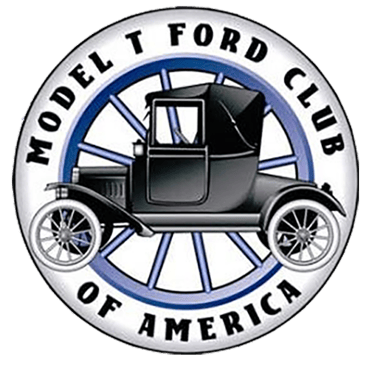
Axle & Rear End
Clean Off Grease on Frame and Brakes
Rub off with a rag dipped in clear turpentine and polish with crude oil. Do not let the turpentine stay on any longer than necessary.
Greasing the Universal Joint
All mechanics know the amount of time that can be wasted in turning down ten or twelve cupfuls of hard grease into the universal joint, especially when the operation has to be repeated on many cars in the course of the day’s work.The mechanic should cut off the head of a cylinder head bolt, and weld this head onto the top of a grease cup cap. This cap can then be turned with a speed wrench and used for filling up the universal joint, after which the regular cap is replaced.
Helicoil – The Hard Way
If it is possible, THAT’s the way it will be done. Example – Front Axle Threads – On my car, they were almost nonexistent, therefore enters my first Helicoil experience. I’m sure those who know me are saying – this article really needs to go no farther – However, it does.
My ever faithful brother volunteered to assist me (I really assisted him) in cutting the threads and in sorting the coils – “Beautiful Job”. Back home, the assembly is started (spindles are already rebushed. The new bolt goes through the top part of the axle, through the spindle and threads into the bottom of the axle. Boy, HOME FREE, slicker than a flat June but, I thought, and that’s when someone turned on the fan.
The bolt head had stopped 3/8 of an inch from the axel, and being from a “if it don’t fit – force it” family tat’s exactly what happened. The harder I turned, the harder it was to turn. Of course, while this was going on the axel was attached to the frame. After a couple of turns, the thought occurred that the bottom axel should receive an inspection. YEP, you guessed it, while standing on my head, two rings of the coil were looking at me. Well, I’ll just back the bolt out and call Prestley to see what I did wrong. I don’t mind calling Prestley because he has such a diplomatic way of telling you.
After two turns of the wrench everything came to a halt again. And still being from the same family I managed to turn the bolt two more turns. At this point I didn’t need Prestley to tell me I was in deep trouble. I just didn’t know how deep.
What had happened was the end of the Helicoil stuck into the bolt and the back of the threads and I was in the process of threading the coil back through the brass busing of the spindle. At this point my logical solution was to take the axel off the car – into the vice – back the coil clean through bushing. But after that was accomplished thence the end of the bolt was, with the coil still hooked tight in the spindle, between the bushings sill on the axel. HA!!! Cut the bolt in half and knock the stuck half out with the ruined busing – GREAT!!! My hacksaw went across that bolt like a BB on a marble floor.
Ever faithful – white hat brother enters again – cuts the bolt with his belt sander, we know the bolt out and HAY! I made it back to ground zero.
But now what … I call the nice folks at Bob’s Antique Auto Parts to complain that the threads did not go up the bolt far enough. Bob explained that the threads of the axel stop about 1/4 of an inch from the edge on the inside of the axel. The smooth part of the bolt just above the threads should snug into this area for additional support.
And sure enough, with a new bushing, new bolt, and a new Helicoil – recessed 1/4 inch – and a few beers everything worked out just fine – THE HARD WAY. Pete Cobb.
Housing Cap Removal
If you have trouble getting the caps which hold the outer felt on the "T" rear end to stay on, slot them with a hacksaw and use a hose clamp around them. Nolan Renfro (198?)
Removing Front Axle King Pin Bushings
If you are rebuilding the front axle on your T, the king pin bushings may be removed by clamping the spindle in the vise and using a pipe wrench to unscrew the bushing. This works on nearly all spindles because the machine marks are fairly deep and act like a coarse thread.
Prior to pressing the new bushings into the spindle, ream them to the new shaft size. This should leave the hole large enough for the reamer pilot to enter after they are pressed in. To prevent scarring the spindles, pad the vise jaws. (Hugo Richter 1984)
Repairing the Ford Rear Axle
When rebuilding a Model T rear axle, the outside rear axle bearings receive little attention. The metal cups over the ends of the rear axle, which holds the felt seal (or new neoprene seal) often become oversized and fit loosely over the axle housing. I have found that even new replacement cups have a tendency to become oversized after removal and replacement a few times. The solution to this problem is relatively simple: slot the sides of the cup in four places with a hack saw (only cut about 1/2 inch into the cup) and use a strap type radiator hose clamp around the outside of the cup to hold it in place. This allows the felt or neoprene seals to fit tighter and allows for easy removal when necessary.
Another messy task when maintaining a Model T rear axle is filling the grease cups for the outside bearings, and then lubricating the bearings by screwing down the grease cups. The solution to this messy job is also quite simple. Go to your local auto parts store and ask for replacement grease fittings with a 1/8th R pipe thread (this is the same thread size as the grease cup fitting itself. Take the base of the grease cup and thread the INSIDE of the grease cup base with a 1/8 R tap. Then take the new grease fitting and screw it into the base of the old grease cup. Screw the base of the grease cup into the axle housing, grease the bearing if necessary, and screw the grease cup lid onto the base.
What you have is an original appearing grease cup with a modern grease fitting installed, which can be easily lubricated with a modern type of grease gun. The mess is over!! (Russ Furstenow, From T-Time in Canyon Country April 2000)
Ruckstell
Model T Ford differentials, particularly Ruckstell, will be the subject this month to along with the various Ruckstell seminars scheduled. Where can I find a Ruckstell Axle and how much should I give for one are questions most often asked. These are hard questions to answer. If I run across one for a good buy, I buy it. By a 'good buy' I mean one that looks to be all there, small drum or large, for around $250 (without drive shaft). From there the price goes UP! Generally about $500 will get a useable one. 'Useable' meaning it could be run for awhile, but to put it in prime condition, a month's work and about $300 worth of available parts and perhaps a couple trips to your local machine shop will be required. Most rebuilders favor a 3x2 Ring and Pinion ratio, and there goes a hundred bucks to start. The unit is well worth the effort when completed and should last indefinitely and will increase in value as well as making driving the T safer and more enjoyable. The Ruckstell is the best multi-speed for the Model T. (Those were the good ole' days ... Ed)
Lubrication of the Ruckstell: Use 1 quart of 250W or SAE 140. Note the W and SAE. 400 W is a little on the thick side for proper lube of the planetary gear pins. Some T parts dealers recommend using 2 quarts of 400 W -- too much and too thick. Also, some recommend SAE 90 being thick enough. I don't think so. The 250 W or SAE 140 is all I will use, and it's proven in many thousands of miles of service.
Check the quantity of the lube at least once a year or more often if you drive a lot. Don't be surprised if your differential case is over-full and you have to let some drain out when the plug is removed. Engine oil has, of course, run down the drive shaft tube and diluted the differential lube. The first sign of too much lube in the differential is when the brake drums start to throw oil out of them. Assuming the ball cap bushing is not overly worn, same for bushing behind the U joint, about all you can do is keep the U joint cavity filled with grease to act as a dam. Not wheel bearing grease, but rather, chassis lube - so the U joint will receive proper lubrication. Don't allow the differential lubricant to become overly diluted, that is, more than a few ounces of engine oil - if so, replace with new lube. Since there is no drain hole, it must be siphoned out - heating the center section of the case helps.
Several have told me about the 'Neutral' their Ruckstells have. Ruckstells don't and were not designed to have a 'neutral.' They do, however, have a point where they are neither in low (Ruckstell) or high. They can't operate in both gears at once. The shifter does not have a neutral either and if they are working properly are either in low or high position - nothing in between. (I have seen a type of shifter handle that had a detent or notch to hold the shifter mechanism on the differential case in a 'neutral' position for some special purpose I suppose. If your Ruckstell has a 'neutral' you've got problems and compete overhaul is indicated.
It seems about one in ten Model T drivers fully understand the shifting operation of the Ruckstell. More damage is done to a unit by these ham-fisted individuals than by anything else. Generally, it's best to shift them when the T is moving and two fingers is all that's required, releasing the clutch - NOT pushing low band. The details of the throttle setting, etc., are too lengthy to go into here, but keep in mind, until you understand exactly how the unit operates, don't risk destroying it. Who knows, perhaps we need a Seminar on 'Driving with the Ruckstell.' (Bob P from the 1981 Pedal Pusher)
Tapered Roller Bearing for the Ruckstell
The bearing number P-211 used in the Ruckstell is a ball bearing, New Departure No. 0212, or equal. A good tapered roller bearing will provide more reliable service. For interchangeability Timken inner race or cone no. 39236 cone and cup no. 39433 will work.
Regardless of which kind of bearing is used, the inner race should be a very light press fit on P-139 bronze end plate. I have seen and tried using a bronze end plate which had the hub knurled to establish a suitable fit. This is quite unsatisfactory. The knurling cannot adequately carry the load, and the bearing inner race will loosen in a very short time. If you should receive a new bronze end plate with the knurled hub, refuse it. It will not last very long. (Hugo Richter)
The Model T Ford and the Microwave Oven (Greasing the T Rear End)
How many times have you tried to add differential grease to your "T" rear end, only to end up with more on the outside than on the inside? That small funnel you made from your wife's kitchen aluminum foil will work much better if you'll warm, thereby thinning the lubricant before trying to add it. This is particularly helpful if your using the heavy 140 weight.
There are many ways to accomplish this but the slickest (no pun intended) is with the help of your microwave oven. Start with a small amount, 2/3 cup, in a non-metallic container. A cream pitcher from a discarded melmac dish set works great for me. You'll have to experiment with the amount of time and temperature setting for your microwave. Start with a low temperature and short time setting (20 seconds) until you get it right. Your wife's assistance (and permission) may be helpful at this point. Warm to the temperature of sipable coffee and it will pour like 20 weight engine oil. Good Luck. (Dave Rosenow)
Tighten T Main Rear Bearing
On page 110 of November 1926 issue, a dealer asks for information on tightening the rear main bearings of improved Fords. We do the work in the following manner: Remove lower pan and extract cotter pins from bearing cap bolts. Also remove wire from cap screws holding fly wheel to crank shaft.
Remove cap screw with socket extension and ratchet handle (only one cap screw need be removed). Remove bearing bolts with special wrench, or (if no special wrench is available) take Ford wrench No. 5Z-153 and bend handle, at about a 15 degree angle, 3 or 4 inches from socket end. After making proper fit of bearing cap, replace fly wheel cap screw and require.
If there are shims under the bearing cap, it may not be necessary to remove the cap screw from the fly wheel. Just loosen bolts, pull out sufficient shims, and retighten bolds. (Contributor Unknown)